Precision machining where accuracy, reliability, and performance are paramount
CNC Machining is often the most effective process for repeatable, tight tolerance, production components. Vaupell utilizes 3, 4, and 5 axis, conventional and high-speed CNC equipment with state-of-the-art CAM Software. We use it to produce machined parts and patterns in an endless variety of materials, including plastics, aluminum, steels, titanium, and composites.
Many years of experience combined with our EDM and 5-axis capabilities have resulted in Vaupell’s reputation as a shop that routinely produces quality parts at high volumes. We utilize our 3, 4, and 5 axis machining centers to machine both metal (aluminum, steel, titanium, etc.,) and plastic materials. In addition, Vaupell Machining is supported by our quality department with full CMM capability.
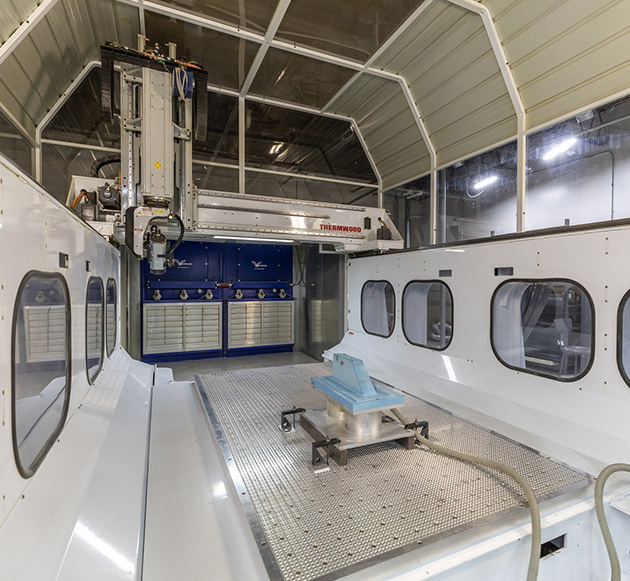
Mill Turning
Complex geometries on round parts using CNC mill turning. This in-house ability of performing both milling and turning using a multitasking machine offers several advantages in modern manufacturing such as: improved efficiency, enhanced accuracy, reduced lead times, cost savings, ability to create complex geometric shapes, ability to accommodate diverse production requirements, better workflow, and shorter setup times.
EDM (ELECTRICAL DISCHARGE MACHINING)
EDM is a non-traditional machining process that utilizes electrical discharges to remove material from a workpiece. This process offers several advantages, making it suitable for various applications. The choice to use EDM should be based on the specific requirements of the project and the materials involved.
3&5 Axis Machining
The choice between 3-axis and 5-axis machining will depend on the specific requirements of your project. Simple parts with straightforward geometries might be efficiently machined using 3-axis machining, while complex, intricate, or sculptural parts would benefit from 5-axis machining. Consider factors such as part complexity, tolerances, surface finish requirements, production volume, and cost.
Near Net Molding
Near-Net Molding Produces Components That Require Minimal Finishing to Achieve the Desired Outcomes. Near-Net Molding is a hybrid approach to manufacturing that combines injection molding with CNC machining. The concept is a derivative of components that have complex attributes that traditional fabrication methods cannot produce on their own. Near-Net Molding works by injection molding a component that is close to the desired geometry with extra stock on areas that have critical features. After molding a part, it is then fixtured in a machining center, where the critical surfaces and tolerances are executed by precision machining.