Excellence in sustainable aerospace commercial interiors
Vaupell is a global full product lifecycle partner and flagship product supplier to OEM and Tier 1 integrators of aerospace commercial interiors. Interior components and subassemblies are high-visibility products with demanding performance and appearance requirements.
For over 75 years Vaupell has been recognized as a leader in the manufacture of appearance moldings and subassemblies for the aerospace-commercial interiors market. We utilize advanced technologies that reduce waste, weight, cost, and manufacturing processes.
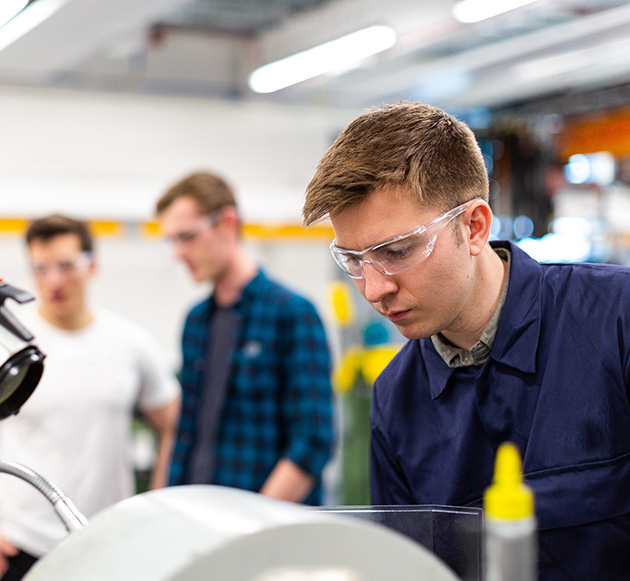
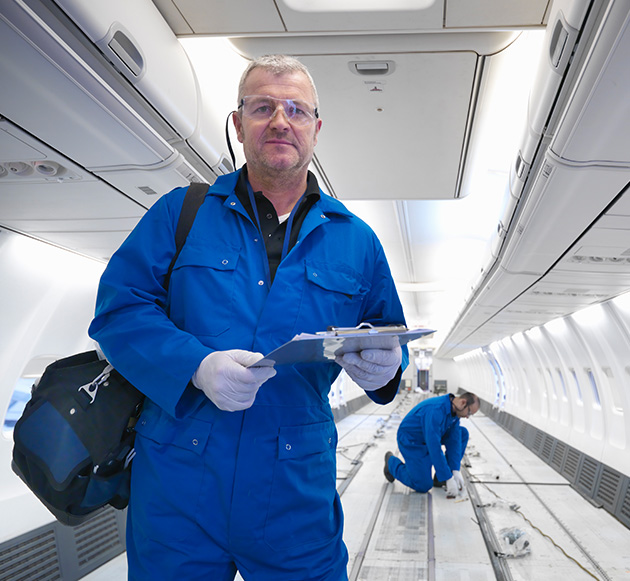
With our in-depth experience and capability, we process high-heat, advanced polymers that meet demanding environmental, dimensional, and appearance requirements of global OEM and Tier 1 customers.
Vaupell has focused on complex assemblies and highly-visible products as well as fuel and hydraulic systems in the aerospace industry.
Product examples:
- Window assemblies
- Cove light panels
- Passenger service units
- Decompression grills
- Literature pockets
- Stow bin trim
- Fuel system valves
- Motor and pump housings
- Seating parts
Case studies
Product leadership examples of aerospace commercial interiors designed, developed and manufactured by our highly skilled team. By designing and developing new materials with improved properties, our material scientists contribute to the creation of advanced technologies, improved manufacturing processes, and enhanced products that are more sustainable for the environment resulting in better buy-to-fly ratios.
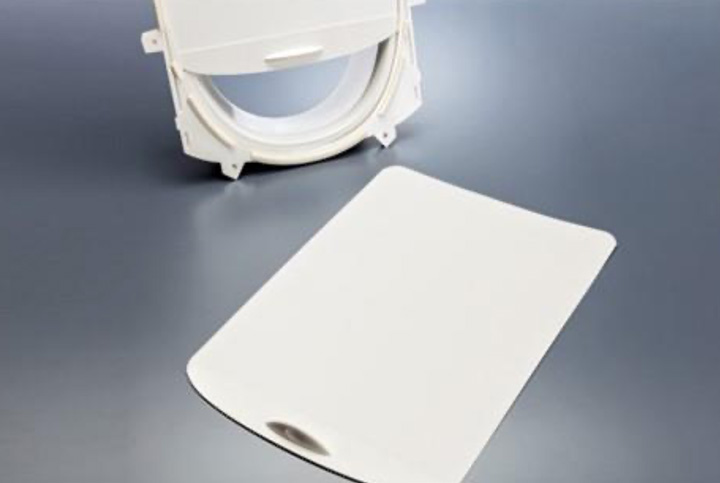
Window reveal assemblies
- Vaupell designed the A350 window unit
- Boeing 737 design concept unitization reducing 12 components to three
- Two component molding
- Improved shade solutions using SB materials (composite shade or thermoplastic formed)
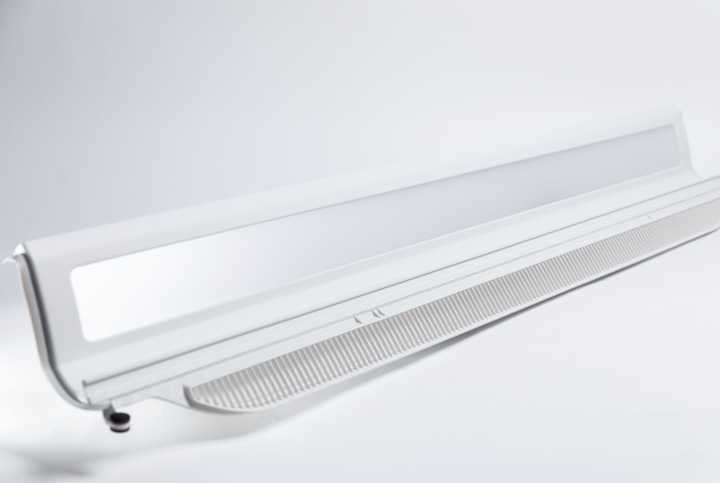
Covelight panels
- Phenolic crush-core panel to thermoplastic thin-walled part (improved recyclability)
- Reduction of ship set weight by 5%
- Reduction in ship set cost of 25%
- 100% delivery and quality performance
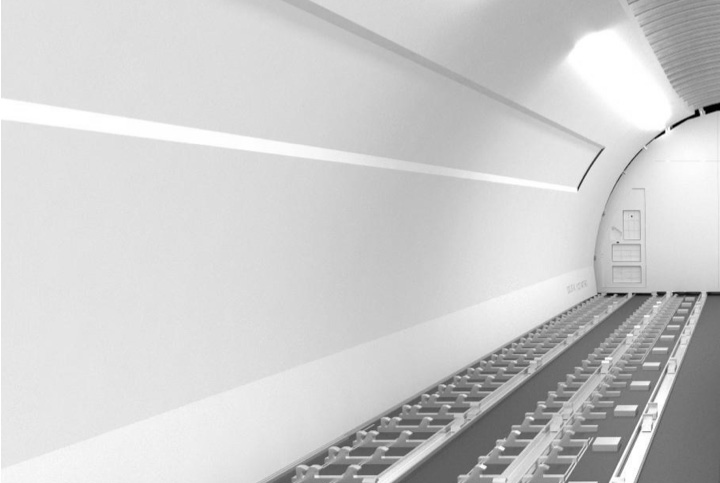
Freighter Main Deck & Cargo liners
- Thermoplastic and thermoset offering
- More sustainable solutions
- Bio prepreg
- Value innovation
- Global locations and local support
- High performance team
Guiding principles for a greener world.
As your trusted partner, we provide comprehensive support and services throughout the entire lifecycle of a product for your aerospace commercial interiors.
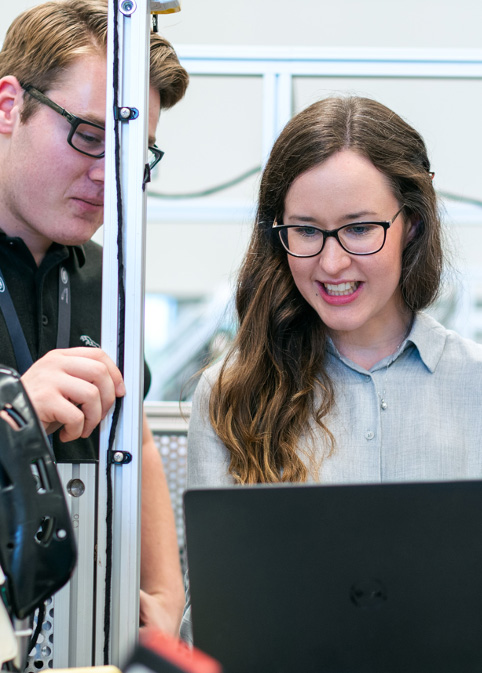
1. Unitization
- Reduce system components
- Elimination of adhesives and fasteners
+
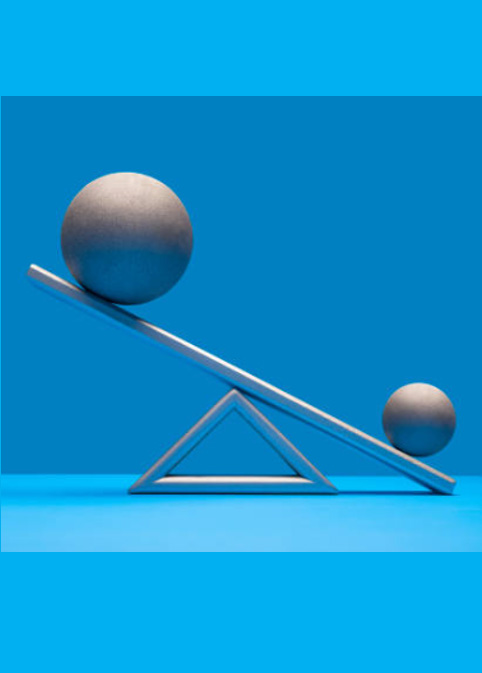
2. Weight reduction
- Metal to plastic replacement
- Thin-walled molding
- Elimination of adhesives and coatings
=
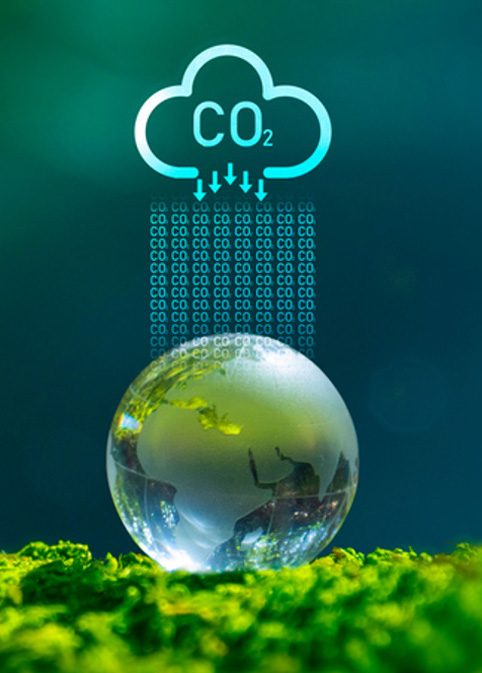
3. Sustainability
- Material identification (transparency and traceability)
- Material lifecycle assessment
- Recycled and bio-based materials
- Material replacement to improve recyclability
A COMMITMENT TO SUSTAINABILITY
In alignment with parent company Sumitomo Bakelite Co., Ltd., we place a high emphasis on the environment and delivering sustainable solutions.
We solve social issues and achieve sustainable growth and value creation under a structure comprised of our Sustainability Promotion Committee (which is chaired by the President) and its subcommittees based on our business philosophy, which esteems the Sumitomo’s Business Philosophy and sets forth our management principles.
We regularly and comprehensively verify the extent of the progress made by these committees, based on which we continuously revise the contents of our activities and actively improve upon them. In aiming for communication with our stakeholders, we widely announce the results of our activities within and outside the company.
Technologies…
that reduce waste, weight, cost, and manufacturing processes.
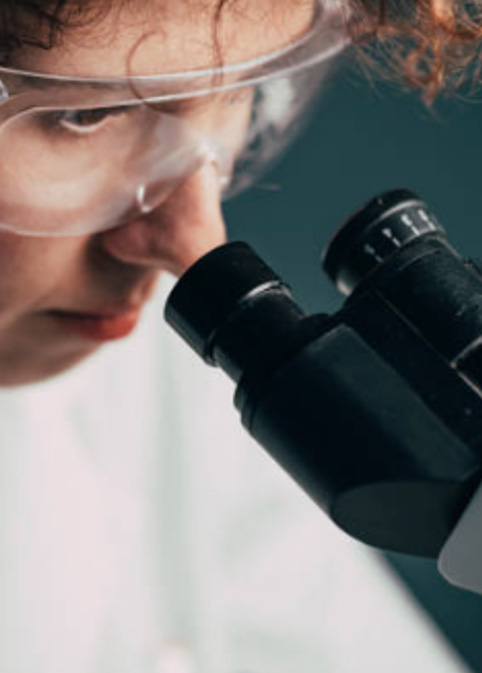
Material science
- Re-using thermoplastic production waste in non-structural products
- PFA replacement of phenolic prepreg and honey comb panels
- Bio-based thermoplastic
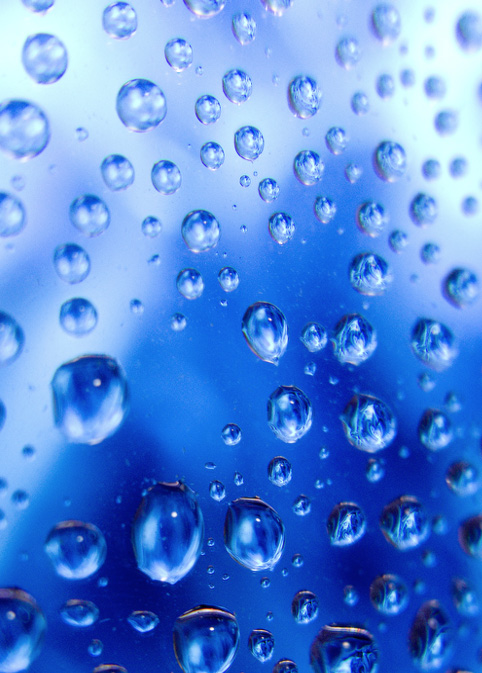
MuCell/RocTool
- Microcellular foaming of thermoplastic resins to reduce weight
- Super-heating/cooling of the injection mold to improve material flow (thinner walls) & improve cosmetics (eliminate coating on cosmetic parts)
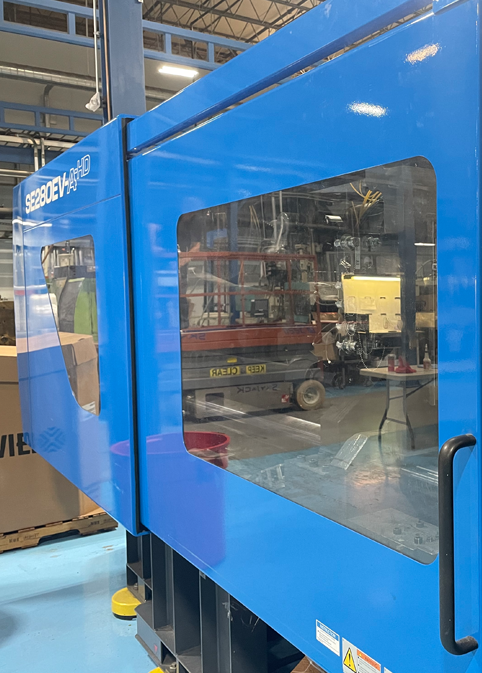
2K injection molding
- Multi-shot molding to eliminate secondary operations & adhesives for bonding secondary components such as seals to panels